Ryobi utilises the Smart Manufacturing Data Hub to unlock value from their data
Founded in 1990 in Carrickfergus, Northern Ireland, Ryobi Aluminium Casting produce aluminium components using the high pressure die casting process for the automotive industry with customers including Volkswagen, PSA Group, Jaguar Land Rover, and Magna. They are part of the Ryobi Group who were founded as a die casting company in Japan in 1943 and have expanded steadily to include multiple manufacturing facilities across Japan, China, USA, Mexico, Thailand, and Europe. Ryobi is certified to ISO 14001 and continually monitors and reduces energy consumption, CO2 emissions, and waste by setting long and short-term goals.
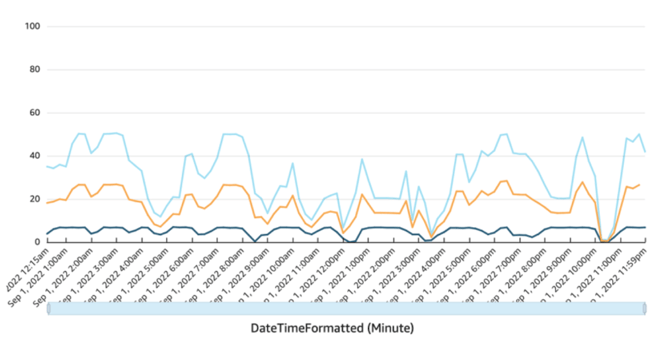
Situation
Ryobi has ambitious low carbon targets and want to get better insights from their energy consumption and production data to identify areas where energy could be saved.
They had already installed a large number of submeters on site to measure the energy consumption or their production equipment, such as die cast machines, at 15-minute intervals. However, these data were not being visualised or analysed alongside other critical business information, such as production outputs, therefore their value was limited.
Solution
The data analysed was summarised at different time granularity, i.e. daily, weekly, and monthly to provide both low-level insights and a higher-level summary to showcase longer-term trends. Data from two different die cast machines, which had made the same parts during the observation period, were included in the analysis to allow a comparison of different equipment.
The dashboard also provided functionality to compare production and energy consumption KPIs between specific days with more granular insights about the energy consumption profile for either day. This allowed the user to compare days with very good performance alongside those with poorer performance and identify potential root causes of inefficient energy use or increased energy costs.