Ritchie Precision makes significant strides in energy consumption management with SMDH Energy Insights.
Ritchie Precision is a specialised precision engineering business located in Scotland, established in 1975. They supply small parts to various markets: Laser, medical, photonics, oil and gas, ultra-sonic, opto-electronic, and scientific instrumentation.
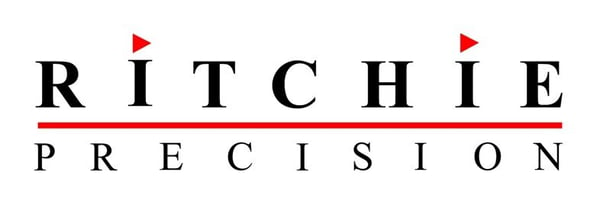
Siutation
In August 2023, Ritchie Precision was facing similar challenges to many other small and medium manufacturing businesses. Their 5-year fixed term electricity contract was coming to an end, and they knew that their cost per kWh would increase significantly.
Furthermore, since their building was leased, it was difficult for them to install any low carbon or renewable technology on their site to counter the increasing energy costs.
As a result, Ritchie Precision was looking to make changes to be able to run their factory as efficiently as possible, reduce consumption and thus reduce the cost of its increasing energy bills.
The company approached the Smart Manufacturing Data Hub to help them explore how the data from their main climate-controlled site could be captured and analysed to monitor and improve their operational efficiency.
Solution
Ritchie Precision undertook a project with the Smart Manufacturing Data Hub to identify any electricity usage that was wasteful. Ritchie Precision uploaded their meter, shift and tariff data into the online data sharing platform where the Data Science team were able to access and analyse it.
Based on the shift details provided by the company, that it operated between 0800 and 1700 and finished early on Fridays, a base usage was calculated and any usage above this during non-working hours was identified as variable load.
Initially the project provided analytics on the electricity usage in the main building, between June 2022 - July 2023, which contained multiple machines making precision parts under controlled conditions. Since then, Ritchie Precision have repeatedly resubmitted updates to their data and have been able to track the reduction in their energy consumption as a result.
For the June 2022 - July 2023 data, we were able to calculate that 11% of all of Ritchie Precision’s electricity use was variable load. In addition to this 74% of their energy consumption was their base load, and by using the SMDH Energy Benchmarking dashboard, the SME realised that this base usage was higher than average for other SMEs.
Period A: 23/10/22 - 01/02/23 (4.5-day work week)
Period B: 23/10/23 - 01/02/24 (4-day work week)
Successes
During our original meeting, we recommended that they undertake behavioural changes, such as asking a member of the team to ensure everything is switched off at the end of the shift, and to educate the workforce on the importance of turning off equipment not in use. As a result of reviewing the graph above they saw how the daily energy consumption dropped dramatically over the Christmas break. They investigated what appliances and machinery were being turned off during the Christmas period but not over the weekends, to see if energy could be saved there. They also started turning off their compressor over the weekend.
As a result of our engagement, Ritchie Precision also implemented a shift change to reduce their energy usage. They trialled this new shift pattern from October 2023 to February 2024, which removed the half working day on Friday. This allowed them to reduce the number of hours a compressor with high energy demand had to run each week. The graphs above compare two time periods, before and during the change in shift.
The charts above show how the mean daily consumption changes during the trial of the new shift pattern, split by day of the week. As expected the consumption on Fridays is significantly reduced in period B when compared to period A, as a result of the shift change. As a result of behavioural changes, including turning off compressors over the weekend, the consumption on other non-working days also decreases in period B.
Once the change of total hours worked is considered, Period B consumed 24% less electricity than Period A, as shown in the chart below.