MANUFACTURING SMARTER
The Smart Manufacturing Data Hub (SMDH) supports small and medium-sized manufacturers to become more competitive by harnessing the power of data.
Digital solutions, expert guidance and funding are available to companies through the hub, allowing them to explore and evaluate their processes, make operational savings, de-risk investments and become more digital savvy.
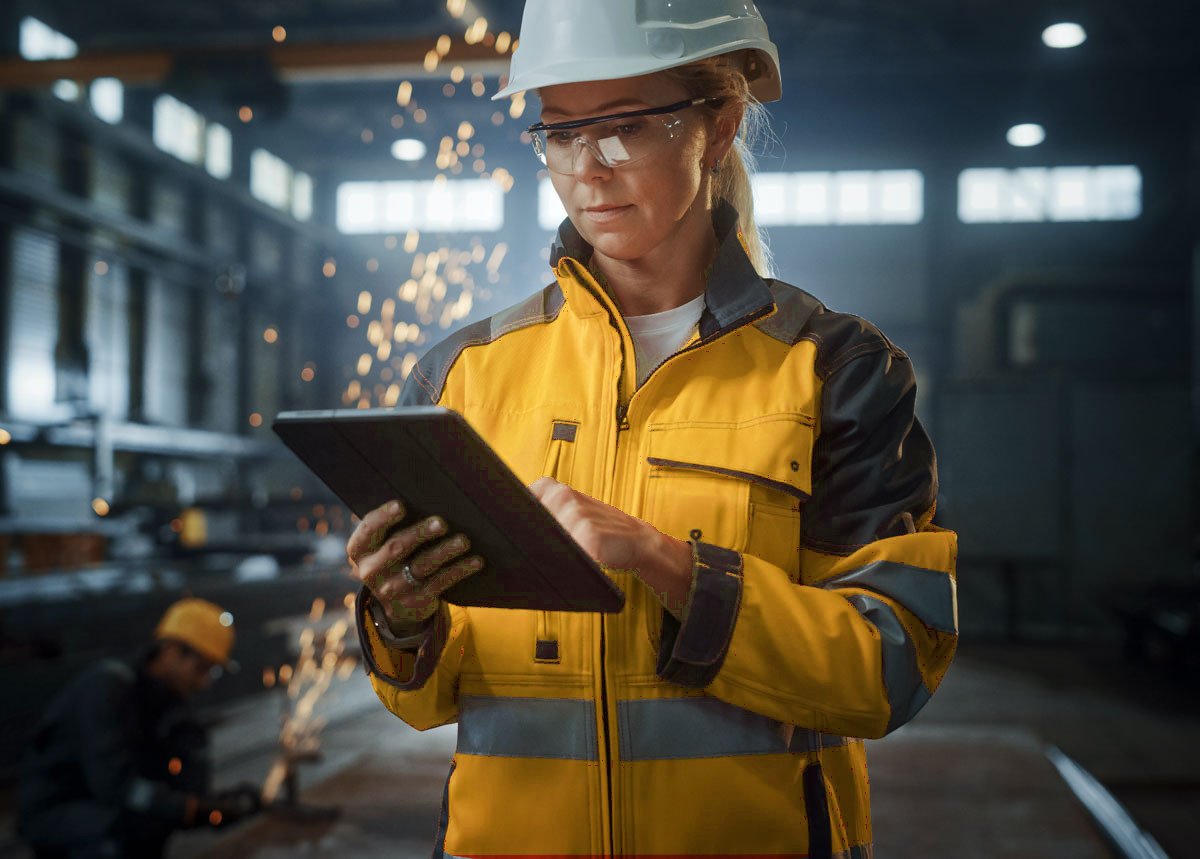
Here’s what we offer
Low Cost Solutions
We have a directory of low-cost data solutions that can be deployed across a range of manufacturing sectors to help you start your data journey.
Virtual Hub
We offer secure data transfer, storage, analysis and dashboarding thorough our virtual hub. You always remain in control of your data without vendor lock-in.
Professional Development
Access training on digitalisation, learning resources and like-minded communities to enhance your workforce skills.
Funding
Companies who work with the Smart Manufacturing Data Hub, are eligible to apply for grant funding on a match fund basis, to allow for further development of digital technology in their factory.
What our customers say
“The Smart Manufacturing Data Hub supported us with a downtime capture solution that allows us to easily access, visualise and analyse our production process from outside the cleanroom, which is a huge benefit to management of the facility and the start of our journey with Industry 4.0.”
“Exitex required a solution for monitoring manufacturing devices on the factory floor to provide insights into preventive maintenance, usage, and productivity of machines. The Smart Manufacturing Data Hub was able to help us to achieve our goals.”
“We had lots of ideas about how we could monitor and record data around our facilities to analyse costs and performance. The Smart Manufacturing Data Hub helped us identify areas of priority, and supported us to perfect the sensors and dashboard, providing an extremely user friendly solution.”
“The Smart Manufacturing Data Hub has helped us to access energy data and utilise this to enhance our production efficiency. Implementing the IoT technology was straightforward, and we are eager to further develop the system to capture and analyse data throughout the entire factory.”
SITUATION
Connex Offsite attended a workshop about the Smart Manufacturing Data Hub and provided a tour of their Newry based facilities to explore how shop floor data capture and visualisation could inform decision making.
SOLUTION
The Smart Manufacturing Data Hub provided Connex Offsite with a IoT sensor solution that would allow them to better understand machine utilisation trends and product costing.
IMPACT
The project has enabled them to track machine utilisation, offering crucial data for optimising power consumption and improving operational efficiency.
SITUATION
Anglia Labels required deeper insights into production metrics such as press running speeds, job costs by customer and label type, and dispatch performance.
SOLUTION
SMDH provided a dashboard that visualised key areas including job costs by customer, press and material, lead times, and dispatch efficiency.
IMPACT
Anglia Labels acknowledged manual data entry errors, which led them to invest in a new Management Information System (MIS) to automate data collection and improve accuracy.
SITUATION
OS Doors has experienced significant growth which has results in a substantial rise in energy consumption. The goal was to identify opportunities to optimise energy efficiency, reduce costs and ensure long-term sustainability in their operations.
SOLUTION
An Energy Insights solution was developed to help optimise energy use. A year of energy data was provided from OS Doors from a single electricity meter along with shift patterns and tariffs. Key insights found that on Fridays, consumption dropped after morning shifts but rose later due to overtime.
IMPACT
This solution has provided OS Doors with insights into their energy consumption during productive and non-productive time in the factory. OS doors will use the insights as a baseline for their upcoming sustainability strategy and are looking at green energy and methods to reduce carbon emissions.
SITUATION
Faced with rising energy costs and a growing focus on operational efficiency, McDonald Water Storage sought opportunities to optimise energy use and enhance workplace safety through air quality management.
SOLUTION
The project involved two distinct yet interconnected analyses: energy monitoring of air compressors and air quality assessment within the facility.
IMPACT
The project yielded significant benefits for McDonald Water Storage, including energy efficiency improvements, enhanced workplace safety and data-driven decision-making. Next steps are to upgrade more air compressors, continue air quality monitoring and explore energy monitoring.
SITUATION
When assessing the condition of their manufacturing systems, Macrete's maintenance staff found that a piece of rotating equipment might appear serviceable externally but could have hidden internal failure issues.
SOLUTION
Macrete decided to undertake a project with the Smart Manufacturing Data Hub that would allow them to monitor assets in real time, using intelligent, wireless, IoT sensors to target machine downtime and energy usage
IMPACT
By setting up alerts, the team were able to detect when abnormal vibrational activity occurred, allowing Macrete to conduct timely maintenance, mitigating the risk of equipment failure and unplanned downtime.
SITUATION
Ritchie Precision were looking to make changes to be able to run their factory as efficiently as possible, reduce consumption and thus reduce the cost of its increasing energy bills.
SOLUTION
Ritchie Precision uploaded their meter, shift and tariff data into the online data sharing platform where the Data Science team were able to access and analyse it.
IMPACT
Ritchie Precision implemented behavioural changes turning off machines and a shift change to reduce their energy usage. Ritchie Precision have repeatedly resubmitted updates to their data and have been able to track the reduction in their energy consumption as a result.
SITUATION
Uform's half-hourly energy data collected over four years was analysed using SMDH's Energy Insights tool. SMDH were able to generate detailed insights and trends in energy usage on a daily, weekly, monthly and yearly basis.
SOLUTION
Uform was provided with three energy dashboards allowing them to pinpoint areas for energy reduction. The analysis helped identify energy-intensive periods and evaluate the effectiveness of various interventions.
IMPACT
Building on the success of this initial project, Uform have engaged with SMDH's Lighthouse partners, Devtank and Output Industries to explore the potential of real-time monitoring for further enhancing data-driven insights, energy consumption and resource efficiency within the factory.
SITUATION
Scott & Fyfe wanted to assess their current energy consumption, measure the impact of energy efficiency measures already implemented, and identify further opportunities for energy savings where possible.
SOLUTION
Using the “Energy Insights” dashboard, the SME was able to see that 68% of their energy consumption was made up of “base consumption”, i.e. energy that is consumed by equipment that is always switched on.
IMPACT
Using the “Energy Impact” dashboard to compare the time periods from April 1, 2022, to January 31, 2023, to the same months of the subsequent year, the SME was able to measure a reduction in electricity consumption of over 1GWh (-37.4%).
SITUATION
Terex sought to lower the effects of escalating energy costs and enhance sustainability. Terex was interested in exploring ways to use current data available to them to better understand when, where and how energy was being used, as well as to identify opportunities for reduction.
SOLUTION
Terex and SMDH conducted an energy consumption investigation, capturing data on usage, shift patterns, and tariffs. The information was uploaded to MDEP, enabling Terex to analyse visual dashboards and extract insights for factory improvements.
IMPACT
The solution provided to Terex enables them to investigate their energy usage and would also allow the company to compare their energy consumption across other manufacturing sites.
SITUATION
Specdrum had to collect and analyse vast amounts of data manually which they found difficult to do in a timely and efficient manner resulting in slow response times to problems and issues revealed by data in the processing plant.
SOLUTION
The SMDH team liaised with Specdrum to install digital and data solutions including the monitoring of power, air quality, oil usage, temperature and pressure. A dashboard now enables clear data visualisations for the team to monitor.
IMPACT
Specdrum can now access real-time data visualisations from several areas of their factory. The automatic alert system from the dashboard ensures management are promptly notified of any potential problems within the factory.
SITUATION
Ryobi has ambitious low carbon targets and want to get better insights from their energy consumption and production data to identify areas where energy could be saved.
SOLUTION
A dashboard was developed to combine data from Ryobi's electricity meters for two different die cast machines with production output and OEE data for the same machines.
IMPACT
Ryobi were very pleased with the dashboards provided by the Smart Manufacturing Data Hub and have realised the value of combining their submeter data alongside production data to establish more insights on key metrics allowing them to invest in an energy platform.
Need clarification?
What is the Smart Manufacturing Data Hub?
The Smart Manufacturing Data Hub (SMDH) is a project funded through Innovate UK to support small and medium-sized manufacturers to become more competitive by harnessing the power of data.
Digital solutions and expert guidance are available to companies through the hub, allowing them to explore and evaluate their processes, make operational savings, de-risk investments and become more digital savvy.
Why do I need data in my business?
Data are often referred to as the new oil, and just like oil, when data are raw and unrefined there is little value. We take data and turn it into timely, actionable insights: information that can guide you towards a decision that will improve your manufacturing business.
When do I need to start my digital journey?
Early adopters of data-driven technology have already started gaining a competitive advantage by substantially lowering operating costs, improving time-to-market, and optimising performance. These benefits will only grow over time.
How can I start to use data?
One small step can start your data journey. For example, you can use temperature sensors measure the amount of heat energy or coldness that is generated by an object or system and alert the user to overheating or insufficient cooling. Through early detection of problems, the user can avoid unplanned downtime, and limit maintenance checks and repairs to when they are actually needed.